Leading Approaches for Optimizing Steel Fabrication Processes for Maximum Efficiency
From meticulous format preparing to accepting cutting-edge innovations, the pursuit for maximum performance in steel construction involves a multifaceted strategy. Let's discover exactly how these approaches can transform steel fabrication procedures, paving the method for unprecedented effectiveness and competition in the industry.
Reliable Format Preparation
In the realm of steel manufacture procedures, effective and critical design preparation plays a pivotal function in simplifying manufacturing workflows and optimizing operational efficiency. The design of a steel manufacture facility straight affects the efficiency of operations, product circulation, and employee productivity. By thoroughly creating the setup of equipment, workstations, storage areas, and material handling devices, business can substantially minimize unnecessary movement, reduce product taking care of times, and optimize the overall production process.
An effective design strategy takes into consideration factors such as workflow sequences, proximity of workstations, material handling routes, and safety policies. It aims to create a streamlined and logical flow of tasks from basic material consumption to the end product send off. Via reliable design planning, business can eliminate bottlenecks, reduce production downtime, and boost the total functional effectiveness of the steel construction procedure.
In addition, a well-thought-out layout strategy makes it possible for much better use of available space, improved interaction in between workers, and enhanced safety and security methods within the facility. In general, investing time and sources in establishing an effective layout plan can yield substantial advantages in terms of increased performance and expense savings for steel construction services.
Advanced Cutting Technologies
Making use of sophisticated technologies in steel fabrication processes boosts precision, efficiency, and overall manufacturing quality. Additionally, plasma cutting modern technology has actually also revolutionized steel fabrication by enabling swift and accurate cutting through electrically conductive materials. By integrating these sophisticated cutting innovations into steel fabrication processes, makers can dramatically raise performance, lower manufacturing times, and eventually enhance the quality of their items.
Automated Welding Solutions
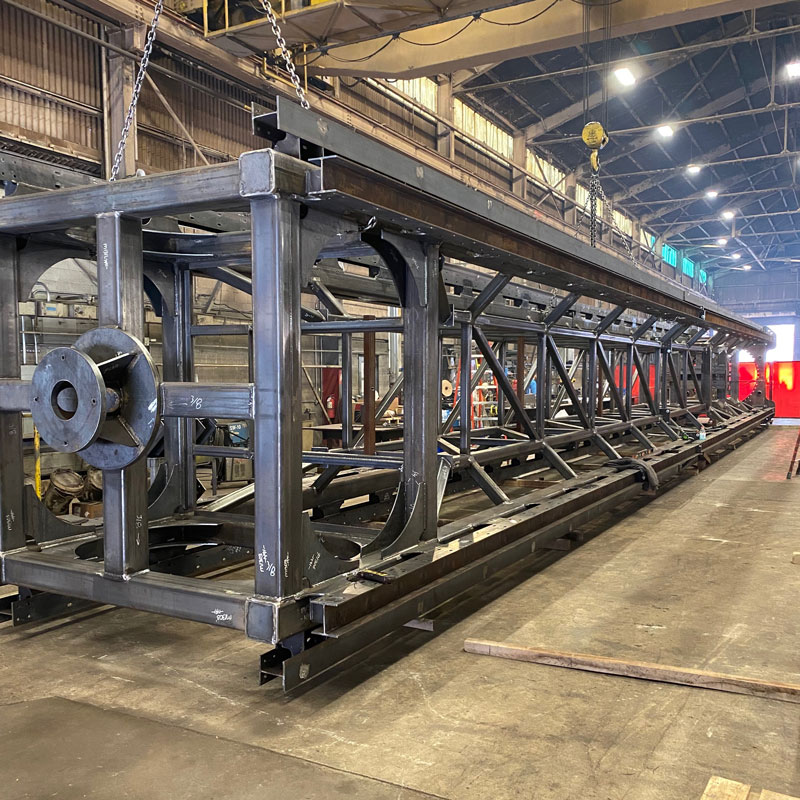
Among the essential benefits of automated welding systems is their ability to preserve a high degree of accuracy throughout the welding procedure. The precision supplied by these systems guarantees that welds are consistent and meet check this site out the required requirements, resulting in more powerful and more reliable metal frameworks. Additionally, automated welding systems lower the danger of human mistake, resulting in fewer issues and rework.
Moreover, these systems can handle complex welding jobs effortlessly, including welding in limited rooms or on curved surfaces. This adaptability makes automated welding systems appropriate for a vast array of steel manufacture applications, from large industrial jobs to complex personalized designs. On the whole, the implementation of automated welding systems in steel fabrication processes substantially boosts performance, quality, and total project results.
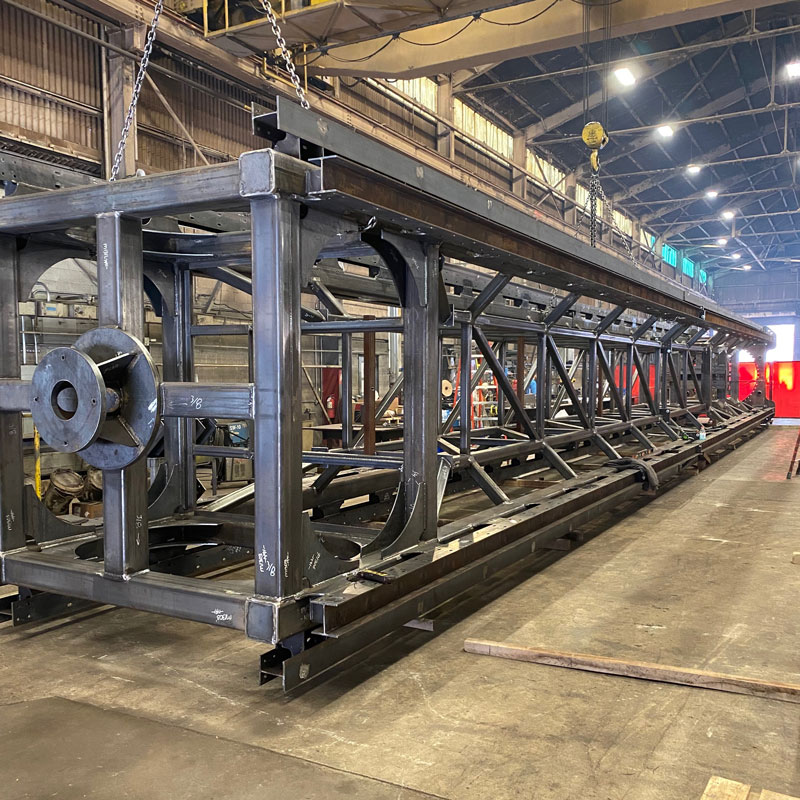
Inventory Management Solutions
Enhancing functional efficiency and streamlining processes, effective inventory management solutions play an essential role in enhancing steel construction operations. By executing robust inventory monitoring systems, steel manufacture business can guarantee that the best materials are available when required, decreasing interruptions and delays in production routines. Using advanced software remedies enables real-time browse around this web-site tracking of inventory degrees, allowing exact projecting of product demands and preventing stockouts or overstock scenarios.
In addition, supply monitoring solutions aid in lowering bring costs linked with excess stock and boost capital by straightening stock degrees with actual need. By classifying materials based on use frequency and urgency, producers can focus on procurement and storage room allowance, further improving operational effectiveness. Additionally, applying barcode or RFID technology promotes accurate supply monitoring and simplifies the surveillance of material motions within the center.
Constant Refine Improvement
To build on the gains made with efficient supply management options, the focus now changes towards driving continual process renovation within steel fabrication operations. Constant procedure improvement is a methodical strategy targeted at improving performance, reducing waste, and enhancing general top quality throughout the fabrication process. By implementing a culture of continual improvement, steel construction business can recognize traffic jams, streamline workflows, and enhance sources to take full advantage of efficiency.
One trick facet of continuous process improvement in steel construction is the regular review and analysis of production processes. This involves gathering comments from workers, keeping an eye on vital efficiency indications, and recognizing locations for improvement. By leveraging data-driven understandings, firms can make enlightened decisions to drive meaningful changes that positively impact operations.
Moreover, adopting lean production concepts can significantly add to refine renovation in steel manufacture. Alpha reo. Strategies such as worth stream mapping, five company, and Kaizen occasions can assist remove non-value-added tasks, standardize processes, and cultivate a culture of technology and continual understanding within the company
Final Thought
In conclusion, optimizing steel construction procedures for maximum efficiency needs cautious preparation, utilizing sophisticated reducing modern technologies, executing automated welding systems, handling supply effectively, and continuously enhancing processes. By integrating these approaches, manufacturers can improve efficiency, minimize prices, and enhance overall performance in the steel fabrication industry.
Through effective layout planning, companies can get rid of bottlenecks, minimize manufacturing downtime, and improve the general functional effectiveness of the steel construction process. Homepage Alpha reo.
Utilizing cutting-edge technologies in steel fabrication procedures boosts accuracy, effectiveness, and overall production high quality. By incorporating these advanced cutting modern technologies right into steel manufacture processes, producers can substantially raise effectiveness, minimize production times, and ultimately boost the top quality of their products.
In general, the implementation of automated welding systems in steel fabrication procedures substantially enhances efficiency, top quality, and general project end results.
One secret element of continuous procedure enhancement in steel fabrication is the normal evaluation and analysis of manufacturing processes. (steel fabrication melbourne)